Reverse Engineering using a non-contact 3D digitizer to reproduce a product without drawings
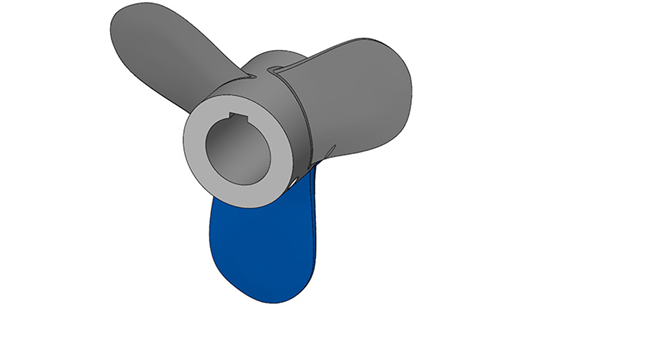
Purpose | Production of Stirring blades |
Processing Method | Stainless Machining and Soldering |
Size | Diameter 300mm Height 110mm |
Delivery terms | One Month |
Quantity | 1 |
Customer’s requests and solutions
A long-time customer asked us for advice on manufacturing a stirring blade. They were frustrated because they had not been able to find a company to do this without a drawing.
Since the stirring blade they were using was adjusted manually by a craftsman, the precise drawing after the adjustment was not available. Therefore, it was impossible to manufacture the exact same product.
Proposal 01 / Reverse Engineering using Non-Contact 3D Digitizer
We proposed the reverse engineering method (* 1) to manufacture the exact same blade as the existing one. We use our non-contact 3D digitizer to measure products when the drawings are unavailable.
*1 Reverse Engineering:To analyze the product structure by disassembling it and observing its movement, and to research manufacturing methods, movement principals, and drawing specifications
Proposal 02 / Structure to assemble the Blades and the Boss which are individually manufactured
We proposed that the blades and the boss be manufactured individually and assembled by welding. We were concerned that the dynamic balance when the blades being rotated may become worse if the parts of the stirring blades were manufactured individually. However, we assured that machining with the 5-axis machining center would enhance the assembly accuracy. The customer approved our proposal.
The number of order was one. The disassembly structure reduced the cost and we received the order, where the customer agreed to pay 200,000 yen for reverse engineering and 300,000 yen for manufacturing.
Point / Reverse Engineering
We used our non-contact 3D digitizer that emits laser beams for the analyzation of the blade shape to obtain its digital data. We designed and manufactured the blades and the boss individually based on the obtained data.
Point / 5-axis Machining Center
Assembling and welding the blades and the boss requires the accuracy of the parts due to the complicated diagonal shapes. However, our 5-axis machining center achieved accurate welding of the parts. The dynamic balance in the rotation that we were concerned about, fell into the range where no adjustment was required.
Achievement / Customer’s Feedback
The customer thanked us for manufacturing the complicated shapes as well as the lack of drawings, where the cost stayed within the budget.
Afterward, the customer ordered more blades of various sizes.
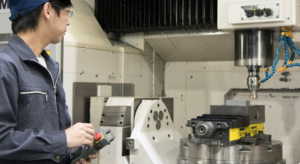